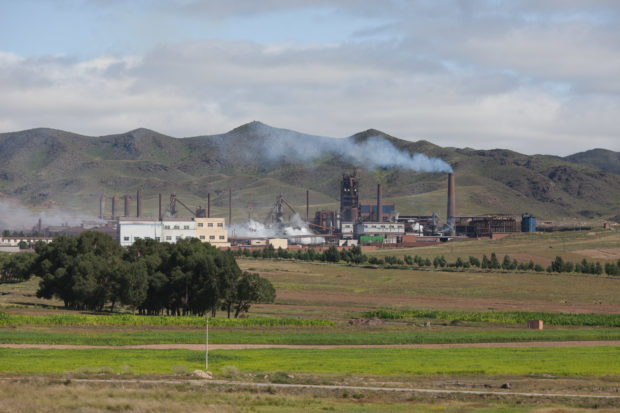
This file photo taken on August 20, 2012 shows a general view of a rare earth refinery north of the inner Mongolian city of Baotou. AFP
NEW YORK — What if China were to cut off the United States and Europe from access to rare minerals that are essential to electric vehicles, wind turbines and drones?
At a time of frequent geopolitical friction among those three powers, Washington and Brussels want to avoid this scenario by investing in the market for 17 minerals with unique properties that today are largely extracted and refined in China.
“The expected exponential growth in demand for minerals that are linked to clean energy is putting more pressure on US and Europe to take a closer look at where the vulnerabilities are and the concrete steps these governments can take,” said Jane Nakano, a senior fellow at the Washington-based Center for Strategic and International Studies.
In 2019, the United States imported 80 percent of its rare earth minerals from China, the US Geological Survey says.
The European Union gets 98 percent of its supply from China, the European Commission said last year.
Amid the transition to green energy in which rare earth minerals are sure to play a role, China’s market dominance is enough to sound an alarm in western capitals.
Cars and turbines
Rare earth minerals with names like neodymium, praseodymium and dysprosium are crucial to the manufacture of magnets used in industries of the future like wind turbines and electric cars. And they are already present in consumer goods such as smartphones, computer screens and telescopic lenses.
Others have more traditional uses, like cerium for glass polishing and lanthanum for car catalysts or optical lenses.
This week the US Senate passed a law aimed at improving American competitiveness that includes provisions to improve critical minerals supply chains, following a similar executive order issued by President Joe Biden in February.
Washington aims to boost production and processing of rare earths and lithium, another key mineral component, while “working with allies and partners to increase sustainable global supply and reduce reliance on geopolitical competitors,” Deputy Director of the National Economic Council Sameera Fazili said Tuesday.
Boosting US production
The best hope for boosting American production can be found at the Mountain Pass mine in California.
Once one of the major players in the sector, the mine suffered as China rose and ate up its market share, aided by Beijing’s heavy government subsidies.
MP Materials relaunched the mine in 2017 and aims to make it a symbol of America’s industrial rebirth, saying the concentration of rare earths at its site is one of the world’s largest and highest-grade rare earth deposits, with soil concentrations of seven percent versus 0.1 to four percent elsewhere.
The company’s aim is to separate rare earth minerals from each other via a chemical process, and then by 2025 manufacture the magnets that industry uses — as market-leading Chinese firms currently do.
The project was supported by the US government, while a Chinese firm is a minority shareholder.
Elsewhere, Australian company Lynas has won several contracts in the United States, including an ore refinery in Texas for the military that was supported by the Defense Department.
Complications for Europe
In Europe, Bernd Schafer, CEO and Managing Director of rare earth mineral consortium Eit Raw Materials, said this month that an “action plan” will soon be presented to the European Commission on how to boost production.
Europe, however, faces a more complicated path to achieving this goal, said David Merriman, a specialist in batteries and electric cars for London-based consultancy Roskill.
“Europe is expected to rely on importing raw materials or semi-processed materials and become more a processing base or recycling base,” he said.
China is expected to remain dominant for some time to come, but Schafer said that if recycling is scaled up, “20 to 30 percent of Europe’s rare earth magnet needs by 2030 could be sourced domestically in the EU from literally zero today.”
The desire to accelerate rare earth production comes amid a shortage of semiconductors, which are essential for the computing and automotive industries and mostly manufactured in Asia.
The scarcity “has caused global manufacturers to think about their supply chain in a new way, and think about vulnerabilities,” a spokesman for MP Materials said, adding that several European automotive and wind power firms are already in contact with the company.